Risk Management: Redefining Factory Cleaning Safety Standards
In the world of manufacturing, factories stand as the crucible of innovation and production. These sprawling facilities are where products come to life, from the smallest components to the largest machines. Amidst the hustle and bustle of manufacturing, it's easy to overlook a critical aspect that underpins it all – factory cleaning. While it may not grab headlines or industry accolades, factory cleaning and safety standards are the unsung heroes that ensure not only the well-being of the workforce but also the efficiency of operations.
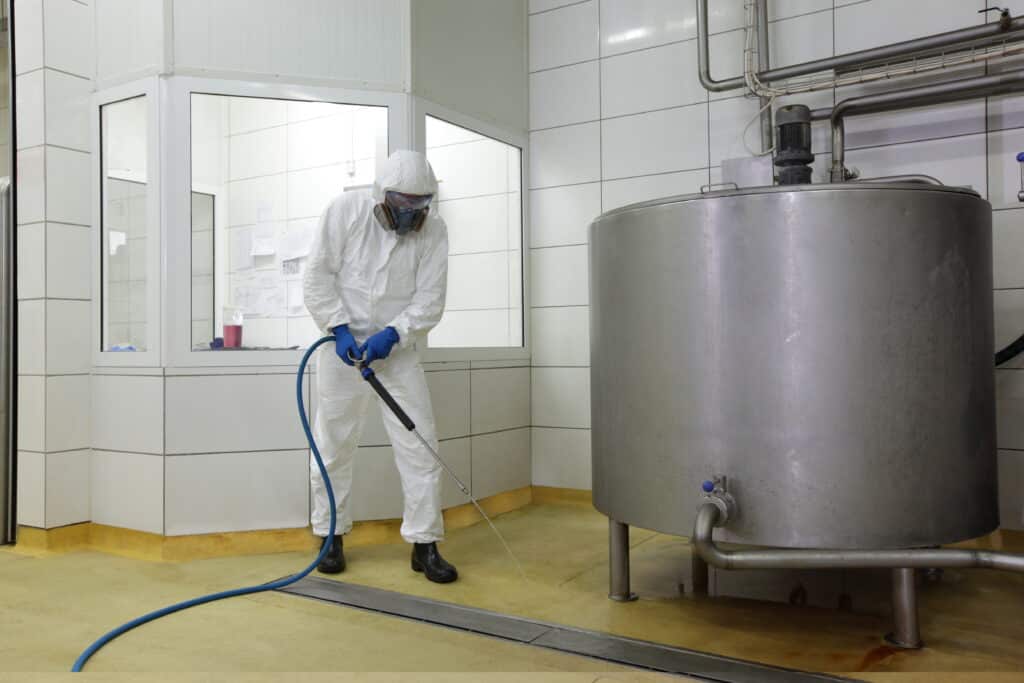
I. The Nexus of Factory Cleaning and Safety Standards
A. Beyond Aesthetics
Factory cleaning goes far beyond appearances; it is the first line of defense against numerous operational risks. When a factory is cleaned and maintained properly, it positively impacts various facets of the operation. Cleanliness, in this context, extends to not just tidiness but to the management of hazardous materials, waste, and safety protocols.
B. The Ethical Imperative
Safety standards are not merely a matter of compliance or regulatory necessity; they are the moral compass of manufacturing. The safety of the workforce is an ethical obligation for any responsible manufacturer. Adhering to safety standards means protecting the employees and the community in which the factory operates. It signifies the commitment to responsible and sustainable manufacturing practices.
II. Embracing Risk Management in Factory Cleaning
A. Identifying Potential Hazards
In the pursuit of risk management, the first step is to identify potential hazards within the factory. These hazards can take on various forms, from chemical spills and electrical faults to machinery malfunctions and more. Identifying these threats is crucial for implementing preventive measures.
B. Crafting Robust Safety Protocols
Once hazards are identified, the next step is to establish safety protocols. These protocols should be tailored to the unique risks present in the factory. They guide employees on the correct procedures to follow in various situations, whether it involves personal protective equipment (PPE), lockout/tag out procedures, or dealing with hazardous materials.
C. Knowledge and Education
Safety protocols are only effective if the workforce understands them. Adequate training and education are vital components of risk management. Employees need to comprehend the risks, know how to mitigate them, and understand the use of safety equipment.
D. Equipping for Safety
The choice of industrial cleaning equipment and tools plays a significant role in ensuring safety. Using industrial-grade equipment and high-quality tools for cleaning and maintenance can substantially reduce the risk of accidents. For example, having spill containment kits and fire extinguishers readily available can make all the difference during an emergency.
E. Regular Audits and Inspections
Incorporating regular safety audits and inspections into the factory's routine helps maintain safety standards. These assessments uncover any deviations from established safety procedures and provide an opportunity for corrective action. Regular audits keep safety at the forefront of operations.
F. Emergency Preparedness
Prevention is crucial, but factories must also prepare for unforeseen emergencies. This. includes having a well-defined emergency response plan. Whether it's a fire, a chemical spill, or a power outage, an effective response can be the difference between a manageable situation and a catastrophic event.
III. Case Studies: Lessons in Safety and Risk Management
A. Factory A: Exemplifying Robust Safety Measures
Factory A, a prominent manufacturing facility, has set an example of prioritizing safety in its operations. Through regular safety audits, extensive employee training, and investments in high-quality cleaning equipment, Factory A has achieved remarkable safety standards. The result has been a notable reduction in accidents and an increase in overall productivity.
B. Factory B: The Consequences of Neglecting Safety
In contrast, Factory B, a similar manufacturing facility, chose to neglect safety standards in factory cleaning. This negligence had severe repercussions, leading to a series of accidents, including chemical spills and machinery-related injuries. The consequences were not limited to financial losses; they also affected the company's reputation.
C. Factory C: The Role of Training and Education
Factory C offers a compelling example of the role of training and education in factory cleaning safety. By emphasizing comprehensive training for employees, particularly in handling hazardous materials, Factory C significantly reduced the number of accidents and near-misses. The commitment to ongoing education played a direct role in enhancing employee safety and operational excellence.
IV. Conclusion: Prioritizing Safety in Factory Cleaning
In the world of manufacturing, safety standards in factory cleaning are indispensable. They go hand in hand with productivity and well-being. These industrial cleaning standards extend beyond cleanliness to encompass risk management, training, and emergency preparedness. By identifying potential hazards, establishing factory cleaning safety protocols, providing knowledge and education, utilizing high-quality equipment, conducting regular audits, and being prepared for emergencies, factories can redefine their safety standards and create a secure and productive workplace.
A. Recap of Key Points
- Factory cleaning and safety standards are fundamental for employee well-being and operational efficiency.
- Identifying potential hazards of industrial cleaning and establishing safety protocols are essential components of risk management.
- Proper training, high-quality equipment, and regular audits contribute to safety.
- Emergency preparedness is crucial for responding to critical situations.
B. The Importance of Redefining Factory Cleaning Safety Standards
Redefining factory cleaning safety standards is not just a matter of compliance; it's a path to success. It leads to a workplace where employees thrive, accidents are minimized, and operational efficiency soars.
V. FAQs: Addressing Common Questions In Industrial Cleaning
1. Why are safety standards important in factory cleaning?
Safety standards are vital in factory cleaning to protect workers, prevent accidents, and ensure compliance with legal and ethical responsibilities.
2. What are some common hazards in factories?
Common hazards in factories include chemical spills, electrical faults, machinery malfunctions, and more.
3. How can factories prepare for emergencies?
Factories can prepare for emergency cleaning by having well-defined emergency response plans, evacuation procedures, and communication systems in place.
4. What is the role of training and education in factory cleaning safety?
Training and education are crucial in ensuring that factory cleaners understand safety procedures, can respond effectively to emergencies, and use safety equipment correctly.
5. How can factories maintain safety standards over time?
Factories can maintain safety standards over time by conducting regular audits and inspections to identify deviations from established factory cleaning safety procedures and take corrective action.
Industrial Leaders Trust SCS Group Integrated Services Manufacturing Facility Cleaning Services in Sydney
Industrial leaders in Sydney place their trust in SCS Group for integrated services, including manufacturing facility cleaning. SCS Group is renowned for its expertise in providing comprehensive and reliable high quality cleaning solutions to meet the rigorous demands of industrial and manufacturing environments in the Sydney area. With a proven track record of excellence, SCS Group ensures that your manufacturing facility remains clean, safe, and compliant with industry standards.
SCS Group's manufacturing facility cleaning services encompass a wide range of solutions, including but not limited to:
General Cleaning:
SCS Group's team of professional industrial cleaners can handle routine professional cleaning tasks, such as sweeping, mopping, and dusting, to maintain a clean and organized workspace.
Specialized Equipment Cleaning:
For manufacturing facilities with specialized equipment, SCS Group has the expertise to clean and maintain these machines to optimize their performance and extend their lifespan.
High-Pressure Cleaning:
Industrial settings often require powerful cleaning methods. SCS Group is equipped to handle high-pressure cleaning to remove stubborn grime and contaminants from various surfaces.
Chemical Cleaning:
SCS Group employs safe and effective chemical cleaning methods to tackle grease, oil, and other industrial residues, ensuring a hygienic and safe environment.
Cleanroom Services:
For manufacturing processes that require a controlled, sterile environment, SCS Group provides cleanroom cleaning services to maintain the utmost cleanliness and quality standards.
Compliance and Safety:
SCS Group understands the importance of compliance with industry regulations and safety standards. They work diligently to ensure that your facility adheres to all necessary guidelines and certifications.
Custom Solutions:
SCS Group can tailor their services to meet your specific professional cleaning needs, offering customized solutions to address the unique challenges of your manufacturing facility.
With a commitment to quality, safety, and efficiency, the SCS Group stands as a trusted partner for industrial leaders in Sydney. Their experienced team, state-of-the-art equipment, and dedication to excellence make them the go-to choice for integrated manufacturing facility cleaning services in Sydney. By choosing SCS Group, you can be confident that your facility will remain in optimal condition, allowing you to focus on your core operations with peace of mind.
For more information or to inquire about SCS Group's services, you can contact us directly to discuss your specific requirements and schedule a consultation.